Blogtext
Siebe und Mühlen – Flexibel einsatzbar in (fast) jeder Prozesssituation
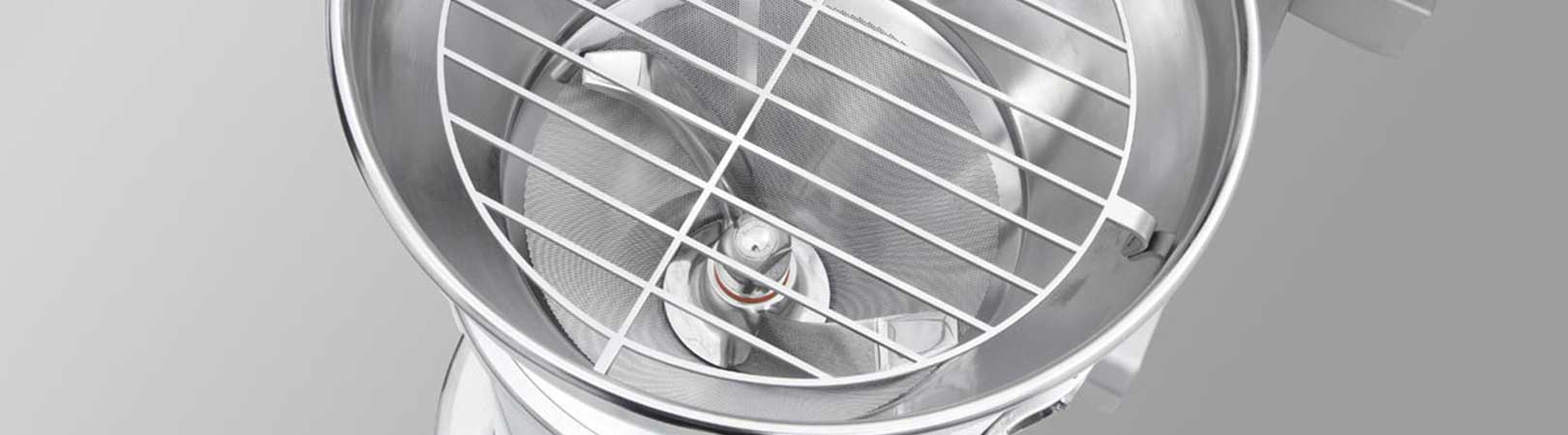
Kegelmühle / Konische Siebmaschine:
Kegelmühlen oder konische Siebmaschinen werden zur einheitlichen Größenreduzierung von pharmazeutischen Inhaltsstoffen verwendet. Des Weiteren können sie auch zum Mischen, Sieben und Dispergieren genutzt werden. Sie sind in einer Vielzahl verschiedener Größen erhältlich – vom Labormaßstab bis hin zur Anlage mit einer hohen Kapazität.
Im Vergleich zu anderen Zerkleinerungstechnologien am Markt bietet das Sieb zahlreiche Vorteile für die Produktion: Eine geringere Geräuschentwicklung, eine enge Verteilung der Partikelgrößen, eine hohe Design-Flexibiltät und eine höhere Kapazität. So kann bei der Verarbeitung von Materialien mit geringer Dichte eine solche Siebanlage den Durchsatz um mehr als 50 Prozent im Vergleich zu herkömmlichen Mühlen erhöhen.
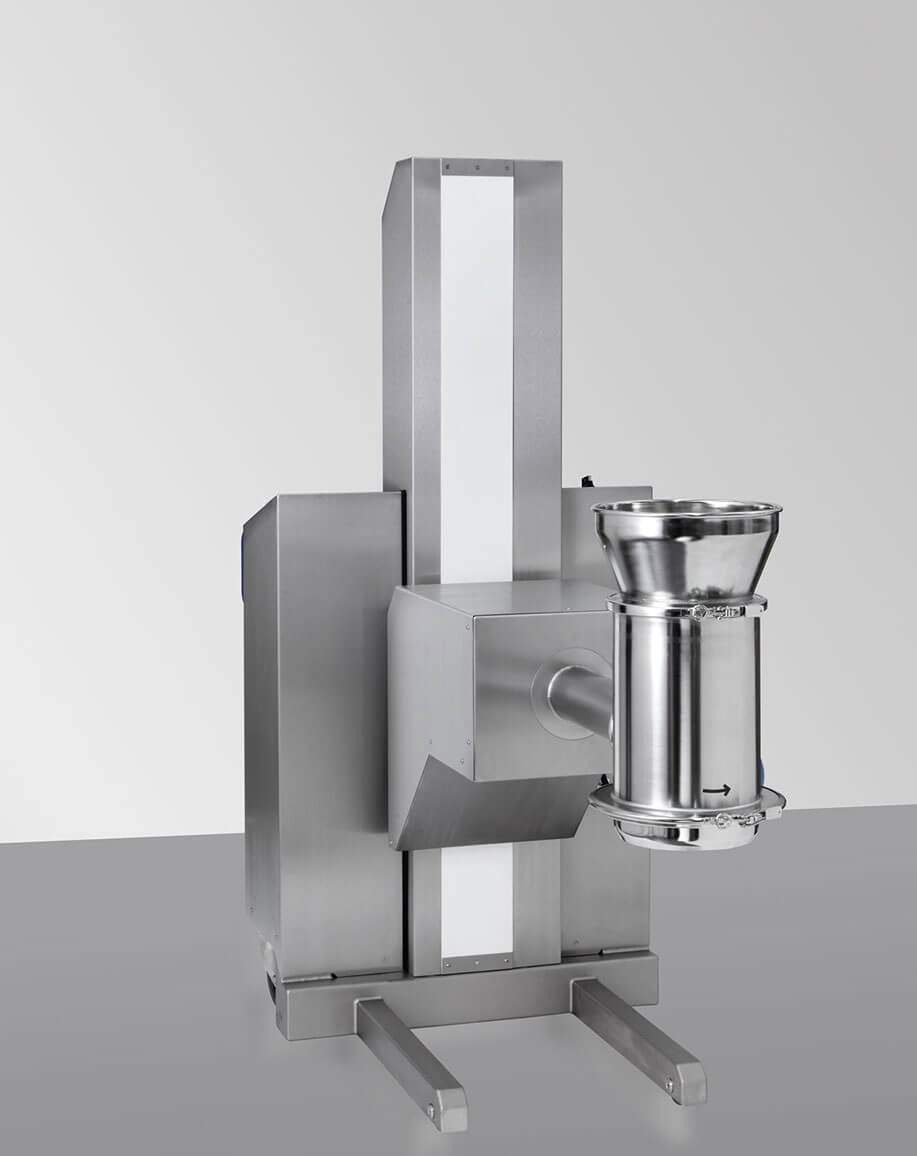
Das patentierte Turbo Sieb BTS der L.B. Bohle Maschinen und Verfahren GmbH (Ennigerloh) wird für die Kalibrierung der Partikelgrößen genutzt und garantiert so eine optimale Partikelgrößenverteilung. Durch den Einsatz verschiedener konischer Siebeinsätze (Lochsieb und Reibsieb) können sowohl trockene als auch feuchte Produkte mit einer Geschwindigkeit von 150 bis 1.500 UpM (Umdrehungen pro Minute) verarbeitet werden. Innerhalb einer Stunde können so Produktkapazitäten von zwei bis drei Tonnen erzielt werden.
Die komfortable Bedienung erfolgt über ein 7“ (Sieben-Zoll-)Touch Panel, das eine Benutzer- und Rezeptverwaltung sowie PDF-Sammeldruckverwaltung ermöglicht und über eine USB-Schnittstelle verfügt. In einer explosionsgeschützten Ausführung ist das Turbo Sieb auch gemäß ATEX-Richtlinien einsetzbar.
Die manuelle Reinigung des Siebes ist dank der reinigungsfreundlichen Konstruktion sehr einfach. Der Siebbehälter kann bequem mit der Kombination aus Bajonettverschluss und Spannring entnommen werden.
Die einzelnen Bauteile sind somit leicht zu reinigen. Optional kann das Siebgehäuse für eine vereinfachte WIP-Reinigung mit Reinigungsdüsen ausgestattet werden, die das Innere des Siebbehälters schnell von Materialresten befreien. Reinigungsdüsen seitlich vom Siebeinsatz und unterhalb des Winkelgetriebes zählen hierbei zum Lieferumfang und werden über einen zentralen Wasseranschluss mit Reinigungsmedium versorgt.
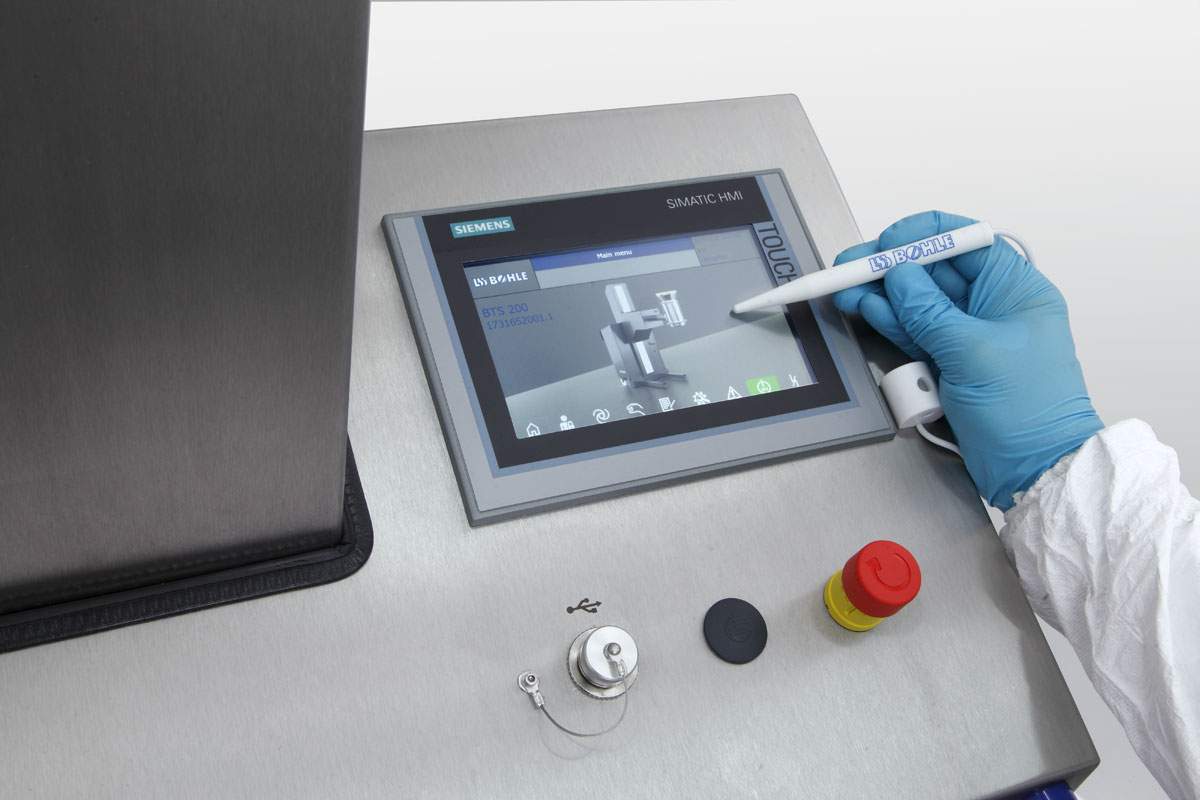
Hammermühlen
Hammer- oder auch Turbomühlen eignen sich sowohl für die Forschung und Entwicklung als auch für die Chargenproduktion oder kontinuierliche Fertigung. Sie zerkleinern Pulver, Agglomerate und Granulate. Besonders häufig werden Hammermühlen eingesetzt, wenn der Anwender eine präzise Partikelreduktion von schwer zu mahlenden Wirkstoffen und anderen Substanzen benötigt. Zudem werden Hammermühlen verwendet, um zerbrochene Tabletten wieder zu zermahlen.
Bereits produzierte Tabletten können bei der Inspektion aus verschiedenen Gründen nicht den Anforderungen des Kunden entsprechen. Kriterien hierfür sind z.B. falsche Härte, optische Mängel oder ein abweichendes Gewicht. Wenn die Tablette nicht der Spezifikation entspricht, kann der Hersteller die Tabletten mit der Hammermühle wieder in Pulver zermahlen und das Material wiederverwenden. Das erneute Mahlen der Tabletten und ihre Rückführung in die Produktion verringern letztlich den Ausschuss und erhöhen die Produktivität.
Hammermühlen, wie die BTM-Reihe (Bohle Turbo Mühle) von L.B. Bohle, können bei Geschwindigkeiten von 600 UpM bis 6.000 UpM, bis zu 1.500 kg/h produzieren. Um dies zu erreichen, ist die BTM mit einem automatischen Dosierorgan (Zellenradschleuse) ausgestattet. Damit kann der Bediener die Mahlkammer gleichmäßig und ohne Überfüllung mit Material beschicken. Außerdem können solche automatischen Zuführvorrichtungen den Pulverfluss in die Mahlkammer steuern. Weitere Vorteile: Die Wärmeerzeugung wird reduziert und der Prozess kann mit gleichen Parametern wiederholt werden.
Der Rotor im Inneren hat zwei Seiten mit unterschiedlichen Funktionen, die Anwendungen mit feuchten oder trockenen Produkten unterstützen. Die sogenannte Messerseite zerkleinert klebrige Produkte. Die Hammerseite wird zum Mahlen von harten, kristallinen Produkten eingesetzt.
Bei der Hammermühle wird die Partikelgröße durch die für die Mühle gewählte Siebgröße bestimmt. Im BTM kann durch den Einsatz von verschiedenen Siebeinsätzen die Materialgröße auf bis zu 0,1mm reduziert werden.
Ein Anwendungsbeispiel
In der Vergangenheit verwendeten Entwickler von Zellkulturen Kugelmühlen, um die Partikelgröße von anfänglichen Mischungen zu verringern. Der Kugelmahlprozess ist zeitintensiv und beruht auf keramischen Kugeln in einem Taumelgefäß, um die Produkte zu Pulver zu zerkleinern.
Nach dem Mahlen einer Charge, müssen Mühle sowie Hunderte von Keramikkugeln im Inneren gereinigt werden. Der Reinigungsprozess kann bis zu einer Woche dauern. In dieser Zeit kann die Maschine nicht genutzt werden und steht nicht zur Verfügung, wenn beispielsweise ein Kunde eine benutzerdefinierte, schnelle Pulvercharge anfordert.
Ein Hersteller solcher Zellkulturen suchte nach einer Mühle, mit der er die Anforderungen seiner biopharmazeutischen Kunden flexibler und effizienter erfüllen konnte. Zudem sollte die Mühle einen geringeren Platzbedarf vorweisen und fahrbar sein. Das Gerät sollte zur Reinigung aus dem ursprünglichen Produktionsraum entfernt werden können, um Platz für weitere Produktionsschritte zu gewinnen.
Der Kunde gab für die Mühle außerdem produktspezifische Anforderungen an Temperatur, Partikel- und Chargengröße vor. Zellkulturen erfordern eine feine Partikelgröße für einwandfreie Auflösungsraten. So müssen bis zu 50 Prozent der Charge kleiner als 100 Mikrometer sein. Darüber hinaus ist das Medium sehr anfällig für Temperaturen von mehr als 37° C, da das Pulver bei diesen Temperaturen seine Bioaktivität verliert.
Nach Sondierung des Marktes wandte sich der Hersteller an L.B. Bohle, um Mahlversuche durchzuführen. Mit der Turbomühle BTM 150 erzielte L.B. Bohle die gewünschte Produktgröße bei einem Durchsatz von 375 kg/h in einem geschlossenen Behälter-zu-Behälter-Mahlaufbau (Inline-Verfahren). Für den Test wählten die Bohle-Experten eine Rotordrehzahl von 6000 UpM mit der Hammerseite des Rotors.
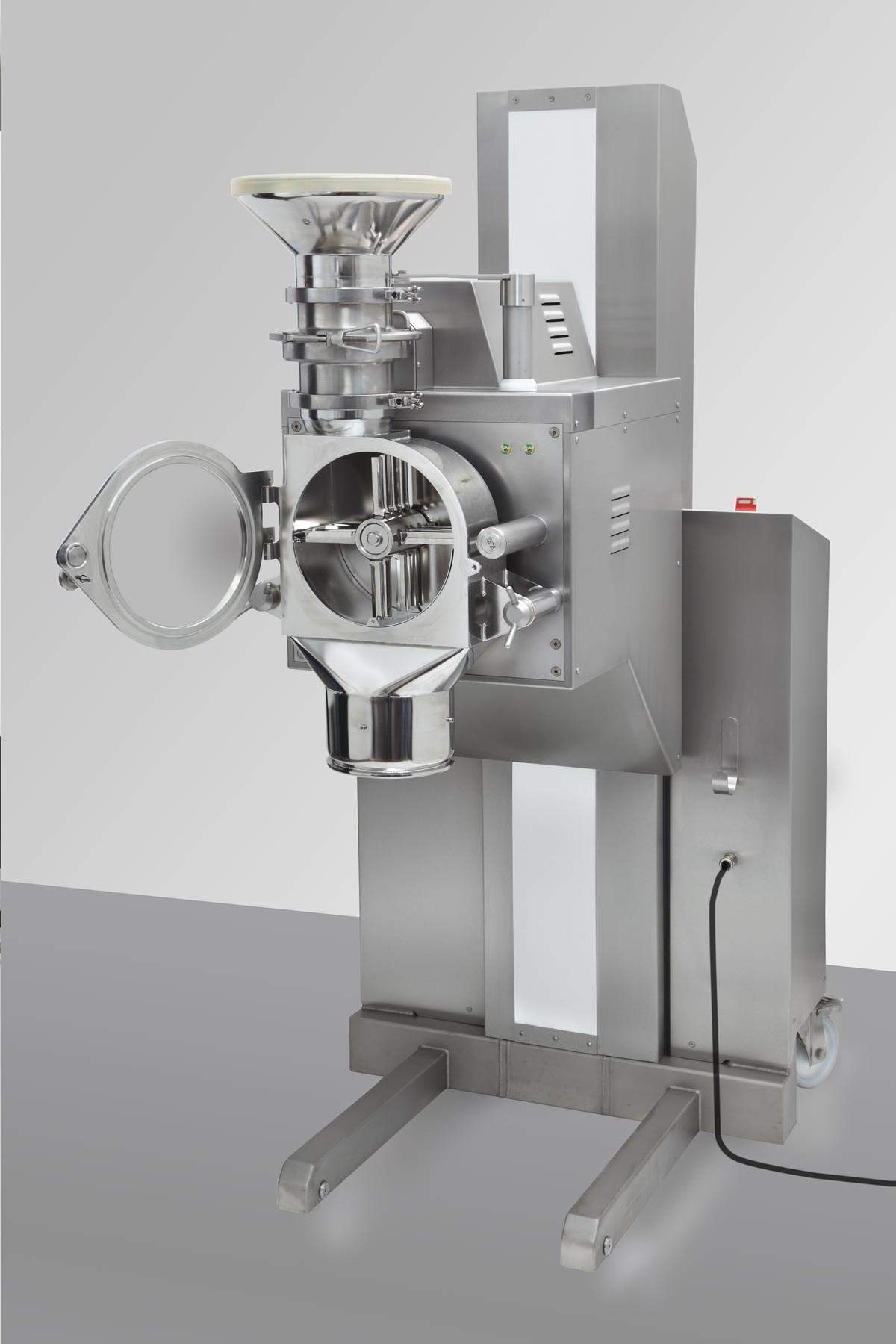
Nach einem Produktionszyklus von 30 kg wurde eine Wärme von ca. 30° C gemessen. Die Mahlkammer bekam einen Kühlmantel, um die Temperaturbesser kontrollieren, die entstehende Wärme abführen und so die Spezifikationen des Herstellers zu erfüllen können. Um eine durch die Kühlung hervorgerufene Kondensation in der Mahlkammer zu verhindern, wird Stickstoff in die Mahlkammer eingeleitet und auch über Filter wieder abgeführt.
Zudem wurde in der Turbomühle ein 1-Millimeter-Siebeinsatz verwendet, der eine identische Partikelgröße gewährleistet wie in der Kugelmühle.
Die präzisen Ergebnisse mit der BTM überzeugten den Hersteller. Er bestellte zunächst eine Hammermühle und später zwei weitere. Nach der Installation der Mühlen hat der Hersteller die Verarbeitungseffizienz erheblich erhöht. So können nun mehrere Batches (z.B. 1000 kg-Chargen) statt nur einer oder zwei Chargen (mit der herkömmlichen Kugelmahlmethode) in einer Woche gemahlen werden, weil das BTM nahezu werkzeuglos sehr schnell zerlegt und gereinigt werden kann.